Common Issues Found in As-Built Surveys
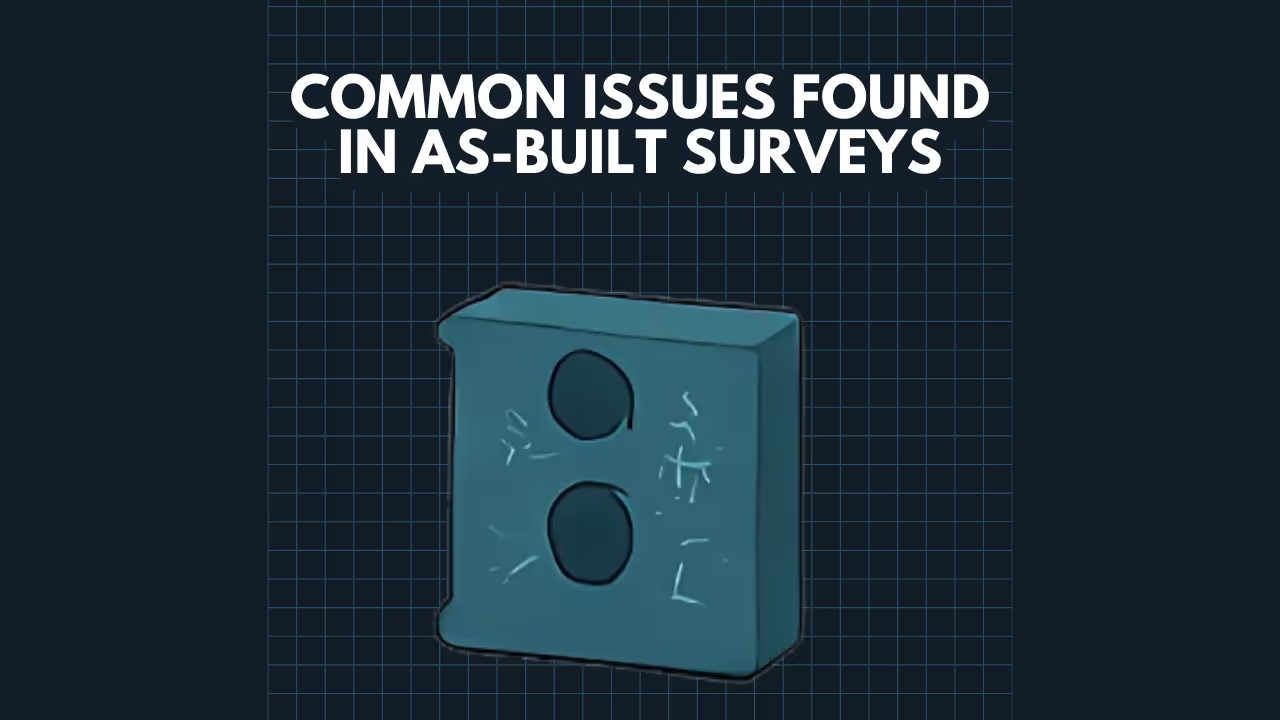
Common Issues and Pitfalls in As-Built Surveys: Ensuring Accuracy and Reliability
As-built surveys are a critical component of any construction or renovation project, providing a definitive record of the final, as-constructed state of a facility. This documentation is indispensable for project closeout, efficient facility management, future renovations, and ensuring safety. However, despite their importance, as-built surveys can often be plagued by common issues that significantly undermine their accuracy, completeness, and overall value. Understanding these pitfalls is the first step towards implementing practices that ensure high-quality, reliable as-built documentation.
Understanding "As-Built Survey" in Context
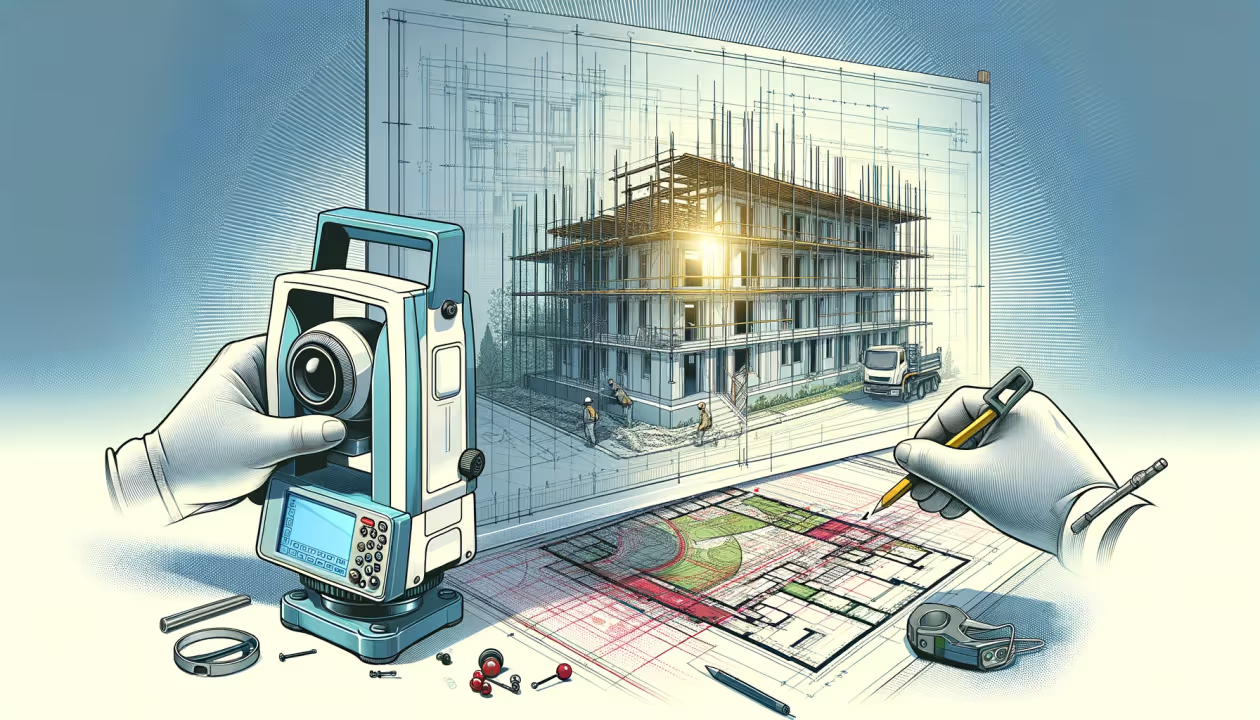
An as-built survey aims to capture and document the precise physical conditions of a project after construction is complete or at significant milestones. This includes the exact dimensions, locations, and configurations of structural elements, architectural features, and critical systems like Mechanical, Electrical, and Plumbing (MEP). The data collected can range from traditional hand-marked drawings and manual measurements to highly detailed 3D point clouds and intelligent BIM models derived from modern reality capture technologies.
Common Issues in Traditional As-Built Surveys
Many of the prevalent issues are particularly common with traditional, manual methods of conducting as-built surveys, although some can affect any approach if not managed properly:
- Incompleteness and Omissions:
- Details Missed: Critical elements, especially those concealed after installation (e.g., in-wall plumbing, above-ceiling ductwork), may not be documented before they are covered up.
- Selective Documentation: Minor deviations from the design might be deemed "unimportant" at the time of the survey but could prove crucial for future maintenance or renovation work.
- Lack of Comprehensive Coverage: Difficult-to-access areas, congested spaces, or complex geometries might be poorly documented or entirely omitted.
- Inaccuracies and Measurement Errors:
- Human Error: Manual measurements using tape measures, laser distos, or even total stations for discrete points are susceptible to human error in reading, recording, or transcribing data.
- Tool Limitations/Calibration: Use of uncalibrated, damaged, or inappropriate measuring tools can lead to systemic inaccuracies.
- Cumulative Errors: In long measurement chains or complex calculations based on manual measurements, small errors can compound into significant discrepancies.
- Outdated Information / Not Reflecting Final Changes:
- Premature Surveying: As-built surveys conducted before all construction work, including final adjustments and installations, are complete will not reflect the true final state.
- Unrecorded Last-Minute Changes: Modifications made on-site after the primary as-built data collection phase may not be captured or communicated.
- Over-Reliance on Design Markups: Simply red-lining design drawings without thorough field verification of every change can perpetuate design inaccuracies into the as-built record.
- Poor Legibility and Inconsistent Formatting (Especially for Drawing-Based As-Builts):
- Illegible Markups: Handwritten notes or dimensions on red-line drawings can be difficult to read or decipher, leading to misinterpretations.
- Inconsistent Standards: Lack of standardized symbols, notations, layering conventions, or scales can make the as-built drawings confusing and hard to use effectively by different teams.
- Lack of Sufficient Detail:
- Generic Representations: As-builts may show the general location of an element but lack the precise configuration, orientation, or specific details needed for future tie-ins, equipment replacement, or detailed analysis.
- Insufficient Information on Connections: The relationships between different systems or components might not be adequately documented.
- Delays in Production and Delivery:
- Time-Consuming Processes: Manual data collection, drafting, and quality checking can be lengthy processes, leading to significant delays in the delivery of final as-built documentation. This can impact project closeout schedules, final payments, and the timely handover to facility operations teams.
- Discrepancies Between Different Trades' As-Builts:
- Lack of Coordination: If individual trades are responsible for providing their own as-built information, there's a high risk of uncoordinated data, conflicting information, and gaps between different systems. A unified, comprehensive as-built survey is often missing.
- Data Accessibility and Usability Issues:
- Physical Document Challenges: Paper-based as-built drawings can be easily lost, damaged, difficult to store, and cumbersome to access, share, or update.
- Outdated Digital Formats: Digital as-builts provided in obsolete file formats may not be compatible with current software, rendering them difficult to use.
- Inadequate Scope Definition for the Survey:
- Unclear Requirements: If the scope of the as-built survey, including the required level of detail (LOD), accuracy tolerances, and specific deliverables, is not clearly defined at the outset, the resulting documentation may not meet the end-user's needs.
How Modern Approaches (Like 3D Scanning) Address These Issues
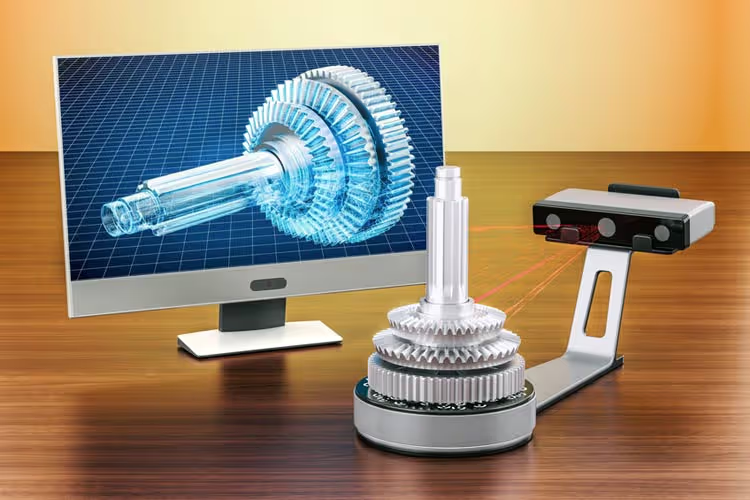
While no method is entirely immune to all potential problems if not managed well, modern reality capture technologies like 3D laser scanning significantly mitigate many of these common issues:
- Completeness and Detail: 3D scanners (e.g., LiDAR, Matterport) capture millions of data points, creating a dense and comprehensive record of all visible surfaces, thus drastically reducing omissions and providing immense detail.
- Accuracy: High-precision scanners minimize human measurement errors and can achieve very high levels of accuracy (millimeter-level in many cases).
- Timeliness & Current State: Rapid on-site data capture allows for surveying closer to the actual completion of work stages, reflecting a more current state.
- Digital Deliverables: The output is inherently digital, ensuring legibility, consistency, and ease of sharing. Accurate CAD drawings or intelligent BIM models can be derived directly from the scan data.
- Data Richness: Point clouds themselves are rich datasets that can be revisited to extract further details as needed, beyond what might be initially drafted.
- Efficiency: While processing is involved, the on-site data capture is often significantly faster than comprehensive manual methods, potentially leading to quicker turnaround of as-built deliverables.
- Unified Data Source: A comprehensive 3D scan can provide a single, unified source of truth for the as-built conditions, which can then be used by all disciplines.
- Accessibility & Management: Digital point clouds and derived models are more easily managed, shared, and archived within Common Data Environments (CDEs).
Best Practices to Avoid Common As-Built Issues
Regardless of the methods used, several best practices can help ensure the quality and reliability of as-built surveys:
- Clearly Define the Scope of Work: Specify requirements for accuracy, Level of Detail (LOD), areas to be covered, and final deliverables in contract documents.
- Schedule Surveys Strategically: Conduct surveys at appropriate project milestones, particularly before critical elements are concealed, and ensure a final survey upon total project completion.
- Engage Qualified Professionals: Utilize experienced surveyors or specialized reality capture service providers, like Data Capture Service, who have the expertise and appropriate technology.
- Leverage Modern Technology: Where appropriate, adopt tools like 3D laser scanning to enhance accuracy, completeness, and efficiency.
- Implement Robust QA/QC Procedures: Establish clear processes for verifying the accuracy and completeness of all as-built information submitted.
- Foster Clear Communication: Ensure ongoing communication between contractors, subcontractors, the design team, and the survey team regarding any changes, deviations, and specific as-built requirements.
- Maintain Diligent Record-Keeping: Encourage all site personnel to accurately and promptly record any deviations from the design plans as they occur.
While as-built surveys are fundamental to the building lifecycle, their value can be severely compromised by common issues like incompleteness, inaccuracies, and delays. By being aware of these potential pitfalls and proactively implementing modern surveying techniques and rigorous best practices, stakeholders can ensure the creation of reliable, high-quality as-built documentation that serves its intended purpose for years to come. Investing in a quality as-built survey process ultimately saves costs, reduces future risks, and enhances the overall management of the built asset.
Ready to explore in more?
Start here:
How Architects Use As-Built Data in Renovation
Top Software Tools for As-Built Documentation
Prefer to Speak Directly?
Experience precision in every project.
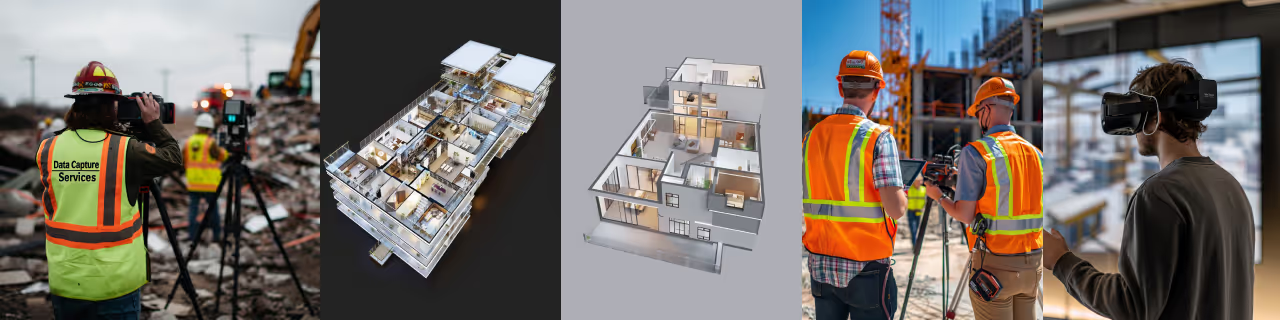